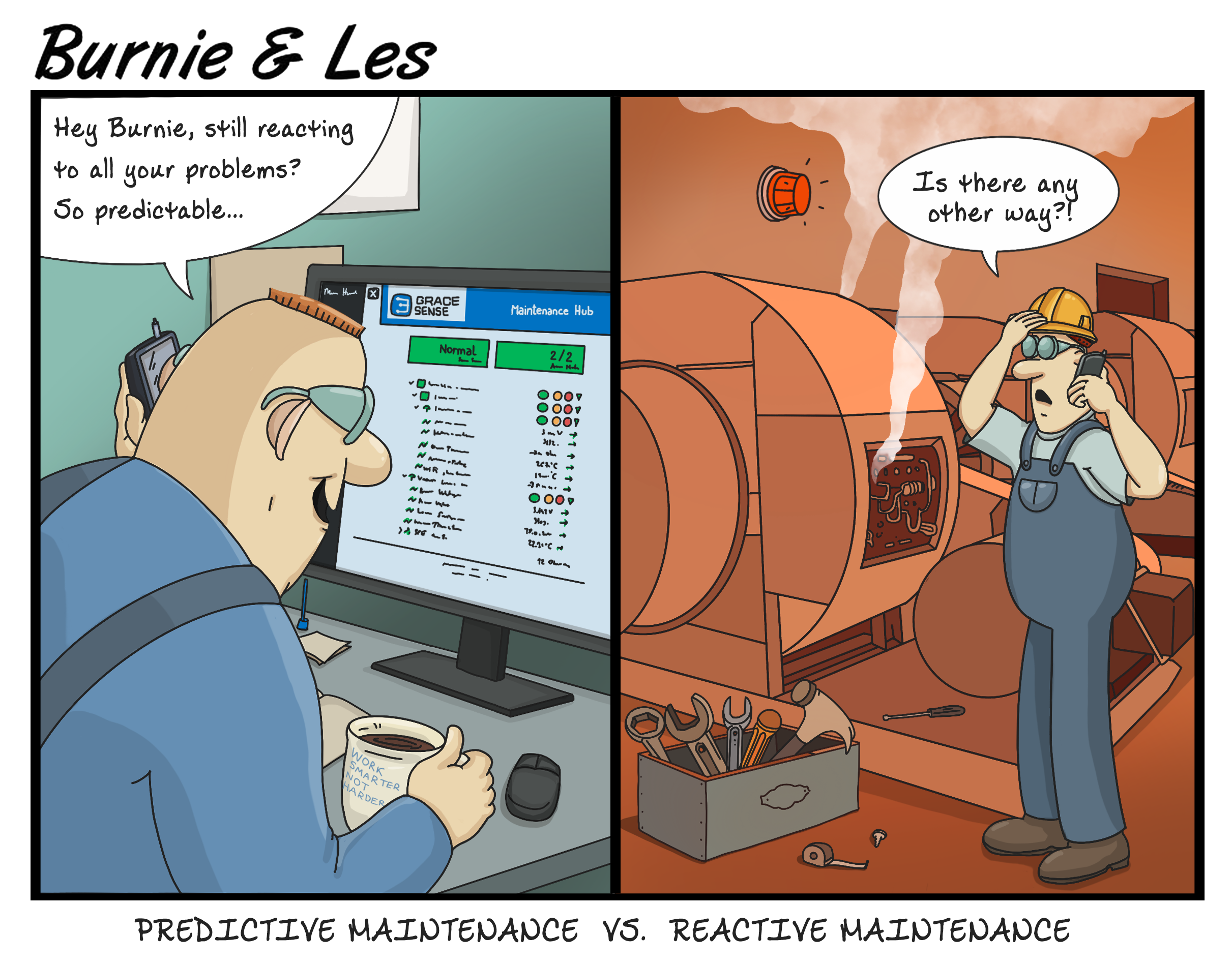
Equipment uptime directly impacts plant productivity and output. An unplanned shutdown due to failure of improperly maintained equipment is among the most costly scenarios a facility can endure. In order to curb this potential major economic loss, many facilities today use a wide array of maintenance methods that include routine physical inspections and condition-based monitoring in an attempt to spot equipment failure before it occurs.
Leading indicators of critical asset failure typically depend on the type of equipment and can include changes in things like vibration, heat, power consumption, airflow, or pressure. By remotely monitoring critical equipment and issuing SMS or email alerts when anomalous or problematic behavior is detected, GraceSense™ technology can help improve productivity and reduce downtime in almost any industrial application.
The GraceSense™ Vibration & Temperature Node was designed specifically with these challenges in mind. By focusing sharply on two of the leading indicators of failure in rotating equipment, the Vibration & Temperature Node continuously monitors critical assets and can alert maintenance personnel in real-time when it detects behavior indicative of bearing, rotor, or shaft degradation.
Once GraceSense™ IIoT hardware is incorporated into a facility’s preventative maintenance program, this technology comes to life through our web-based Maintenance Hub, which is used to configure the system, view current system status, analyze historical data trends, and generate periodic reports. The Hub is also where users can create customizable alert messages with step-by-step remediation instructions designed to allow even new or untrained personnel to address critical issues as they arise.
Nodes share their data wirelessly with any GraceSense™ gateway located nearby where local vibration and surface temperature measurements can combine with other measured data like ambient temperature or current draw. The gateways transfer accumulated field node information into an actionable troubleshooting platform via our Maintenance Hub Cloud and/or your PLC, SCADA, DCS system.
GraceSense™ gateways are all powered by 24-volts and offer configurations for Cloud data transferring via WiFi/LTE as well as control network integration via EtherNet/IP™ & MODBUS TCP/IP communication options. Predictive Maintenance System gateways come in three forms: ControlGate, CloudGate, and ComboGate. The ComboGate configuration allows for both options of communication.
While GraceSense™ components like the Hot Spot Monitor and Vibration & Temperature Nodes can be applied to different types of critical asset applications, they're each designed to strengthen a facility’s preventative maintenance program and empower maintenance teams with actionable insights. Learn more about our GraceSense™ gateway configurations and a bit of history about the Predictive Maintenance System from Grace Technologies CTO, Andy Zimmerman, in the video below:
Over the past decade, the promises of IIoT have been great, but we have yet to see a set of products truly rise up to meet the level of hype surrounding this space. There are good reasons for this: this stuff is hard, the technology is young, and it will take some time to perfect. But that doesn’t help you explain to management why your large IIoT expense is not yet generating any justifiable return on investment.
Fortunately, there is an area in which IIoT is starting to create industry-wide value: monitoring vibration in rotating equipment. For more, check out Andy Zimmerman's whitepaper below: "How IIoT Can Stop Being a Buzzword and Start Creating Value in Your Plant"