WHAT IS A PANEL INTERFACE CONNECT?
A panel interface connector (PIC) is an essential tool for modern industrial controls panels, providing a convenient and safe way to access the systems within an enclosure without having to open the panel door. This innovative technology has revolutionized the way engineers and technicians interact with control panels, streamlining processes, and enhancing safety measures.
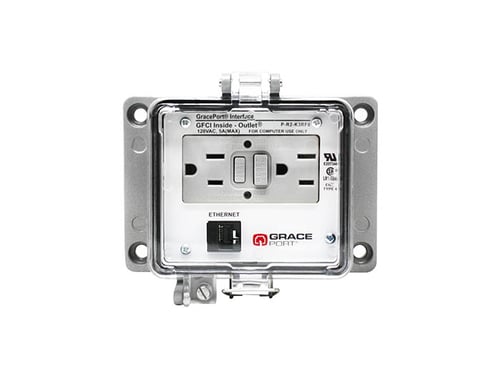
HOW DOES A PANEL INTERFACE CONNECTOR WORK?
PICs allow you to connect to the systems inside an enclosure, like a Programmable Logic Controller (PLC), without having to open the panel door. The PIC is typically mounted on the outside of the control panel and connects to the internal components through a series of cables and connectors.
When a technician needs to connect a laptop or other external devices to the PLC, they can do so by simply plugging into the PIC on the outside of the panel. This eliminates the need to open the panel door, which can be time-consuming and dangerous due to the risk of arc flash or electric shock.
APPLICATIONS OF PANEL INTERFACE CONNECTORS
PICs are widely used across various industries, including:
- Manufacturing: In the manufacturing industry, PICs are commonly used for connecting to PLCs, allowing for efficient programming, maintenance, and troubleshooting.
- Energy: In the energy sector, PICs are used for connecting to control systems in power plants, substations, and other facilities, enabling safe and efficient operations
- Pharmaceutical: In pharmaceutical facilities, PICs are used for accessing control systems in production and quality control processes, ensuring compliance with regulations and efficient operations
- Food and Beverage: In the food and beverage industry, PIC's are used for accessing control systems in production lines, ensuring efficient operations and compliance with food safety standards
- Water and Wastewater: In the water and wastewater industry, PICs are used for accessing control systems in treatment plants, pumping stations, and other facilities, enabling safe and efficient operations
WHY SHOULD I USE A PANEL INTERFACE CONNECTOR?
Using a Panel Interface Connector offers several advantages that can enhance the safety and efficiency of your operations. It enables you to establish a connection with the internal systems without exposure to live electrical components, reducing the risk of arc flash or electrical shock. It allows you to perform maintenance, updates, or troubleshooting while the system is still operational, which can minimize downtime and increase productivity.
ADVANTAGES OF USING PANEL INTERFACE CONNECTORS:
- Safety Enhancement: By allowing access to the control systems without opening the panel, PICs significantly reduce the risk of arc flash and electrical shock, making it much safer options for technicians and engineers
- Efficiency Improvement: PIC's enable quick and convenient access to the control systems, which can streamline maintenance and troubleshooting processes, reducing downtime and increasing overall productivity.
- Simplifies Maintenance: By allowing external access to the control systems, PICs simplify the process of performing updates or modifications to the system.
- Minimizes Downtime: With a panel interface connector, you can establish a connection with the control systems even while the system is still operational, which can help minimize downtime during maintenance or troubleshooting.
CHALLENGES AND RISKS WITHOUT A PANEL INTERFACE CONNECTOR
In an industrial setting, the maintenance of machinery and equipment is a crucial task that ensures the smooth operation of the entire facility. It involves troubleshooting, repairing, and monitoring the equipment to prevent costly breakdowns and ensure optimal performance. However, performing maintenance on industrial machinery can be a challenging and risky endeavor, especially when done without a PIC.
To address these challenges and risks associated with maintenance without a PIC, many industries are turning to PICs as an essential tool for safe and efficient maintenance. PICs provide an external interface that allows technicians to access control panels without opening the cabinet doors. This not only reduces the risk of arc flash incidents but also enables real-time monitoring and diagnostics, leading to faster and more accurate troubleshooting.
Performing maintenance without a PIC can be a risky and inefficient endeavor. By investing in PICs, industries can protect their maintenance personnel from the risk of arc flash, reduce downtime, and increase the efficiency of their maintenance operations.
INEFFICIENCY IN MAINTENANCE
Maintenance personnel often need to open the doors of electrical cabinets to access control panels and make necessary connections. This exposes the internal components to environmental elements such as dust, moisture, and debris, which can cause premature wear and damage. Additionally, when technicians open the cabinet doors to access the control panels, it interrupts the normal functioning of the equipment, leading to downtime and lost productivity.
Furthermore, technicians may struggle to locate the correct connections within the crowded and confined space of an electrical cabinet. This difficulty can lead to longer maintenance times and increased labor costs. In addition, the frequent opening of the cabinet doors increases the risk of accidents, such as an accidental short circuit or a dropped tool, which can cause damage to equipment and lead to costly repairs.
LACK OF DIAGNOSTIC TOOLS
Technicians are also limited in their ability to diagnose issues and monitor equipment in real-time. Since they cannot access the control panels without opening the cabinet doors, they may have to rely on manual inspection and offline diagnostic tools, which can be time-consuming and less accurate than real-time monitoring. This lack of access to diagnostic tools can make it difficult for technicians to identify the root cause of a problem and implement effective solutions.
RISK OF ARC FLASH
One of the most significant risks associated with accessing electrical cabinets without a PIC is the potential for an arc flash, a sudden release of electrical energy caused by a short circuit or an electrical fault. Arc flash incidents can have severe consequences, including fires, equipment damage, and serious injuries or fatalities to maintenance personnel.
By opening the electrical cabinet doors without a PIC, technicians expose themselves to live electrical components and the associated risk of arc flash. Even with appropriate personal protective equipment (PPE), the risk remains high, as an arc flash can cause temperatures to rise to thousands of degrees in a fraction of a second, generating a powerful blast of energy that can throw workers across the room and cause severe burns.
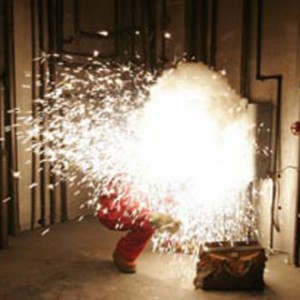
HOW PANEL INTERFACE CONNECTORS PREVENT ARC FLASH
Arc flash is a dangerous phenomenon that can occur when an electric current jumps from one conductor to another, resulting in a sudden release of energy in the form of light, heat, and sound. It can cause severe burns, injuries, and even fatalities.
By allowing you to access the control systems without opening the panel, PICs significantly reduce the risk of arc flash. When you open a panel, you expose yourself to live electrical components, which increases the risk of an arc flash occurring. By using a PIC, you can establish a connection with the control systems without exposure to live components, minimizing the risk of arc flash.
PICs are an invaluable tool for modern industrial control panels. They offer numerous benefits, including enhanced safety, improved efficiency, and the ability to customize configurations to fit specific requirements. By using a PIC, you can access the control systems without exposure to live components, reducing the risk of arc flash and electrical shock. If you're involved in the maintenance, programming, or troubleshooting of industrial control panels, a PIC is an essential tool to have in your toolkit.
CONFIGURATIONS & CUSTOMIZATION
GracePort PICs are not only known for their versatility and reliability, but they're also highly customizable, catering to a wide range of industrial applications. GracePort provides a comprehensive set of options for configuring and customizing their PICs to meet the specific requirements of each client.
- Component Customization: One of the standout features of GracePort's PICs is the wide selection of components available for customization. GracePort offers a wide variety of power options, including international power options, making them ideal for use anywhere in the world. Additionally, GracePort PICs can include data components such as RJ45, USB, and D-sub connectors, among others, enabling you to create a customized solution that fits your unique connectivity requirements.
- Housing Styles: GracePort offers multiple housing styles to choose from, ensuring that you can find the perfect fit for your enclosure. Options include the innovative ThruView Housing, which allows you to see the components inside without opening the enclosure. GracePort PICs are also available in different sizes to fit a wide range of enclosures, ensuring compatibility with both existing and new installations.
- Custom Text and Graphics: GracePort PICs can be customized with text and logos on the faceplate for easy identification. This feature is especially useful for large installations or projects with multiple PICs, making it easier for technicians to quickly identify the correct connection points. Whether you need specific labeling for certain connectors or want to include your company logo, GracePort can accommodate your custom text and graphic requests.
WHY GRACEPORT PANEL INTERFACE CONNECTORS ARE ESSENTIAL FOR YOUR APPLICATIONS
The landscape of industrial maintenance and diagnostics is evolving, and to stay at the forefront, it’s imperative to equip yourself with the most effective and reliable tools. If you haven’t already integrated a PIC into your operations, now is the time to consider the transformative impact it can have on your day-to-day tasks.
Why GracePort? Not all PICs are created equal. GracePorts stand out as an industry-leading solution, meticulously crafted with the user in mind. Here's why making the switch to GracePort is a game-changer:
- Safety First: With GracePort, you can troubleshoot, program, or maintain without ever opening the electrical enclosure. This not only protects your equipment but also ensures the safety of your team by minimizing risks associated with arc flash and electrical faults.
- Versatility and Customization: Every application is unique. GracePort recognizes this and offers an unparalleled range of configurations and customization options, from various components to power options, ensuring your PIC truly aligns with your specific needs.
- Reliability and Durability: GracePort's robust construction ensures longevity and performance even in the most challenging industrial environments. This means less downtime, fewer replacements, and consistent results.
- Seamless Integration: GracePort’s design philosophy emphasizes compatibility and user-friendliness, ensuring that integration into your existing systems is smooth and hassle-free.
By incorporating a GracePort PIC into your operations, you're not just adopting a tool; you're investing in a partnership that prioritizes your safety, efficiency, and productivity. Don't let another day go by without harnessing the full potential of your applications. Choose GracePort and experience the difference.
FAQ
A panel interface connector (PIC) is an essential tool for modern industrial control panels, providing a convenient and safe way to access the systems within an enclosure without having to open the panel door. This innovative technology has revolutionized the way engineers and technicians interact with control panels, streamlining processes, and enhancing safety measures.
Using a PIC offers several advantages that can enhance the safety and efficiency of your operations. It enables you to establish a connection with the internal systems without exposure to live electrical components, reducing the risk of arc flash or electrical shock. Moreover, it allows you to perform maintenance, updates, or troubleshooting while the system is still operational, which can minimize downtime and increase productivity.
Download our free ebook
Making your industrial control panels safer and more productive
- Why Industrial Control Panels (ICPs) pose a high risk and how they increase safety
- The difference between energized work and normal operation in an ICP
- The effect of complacency in your electrical safety programs and how to improve compliance
- How Panel Interface Connectors can improve ICP task productivity by 90%