WHAT IS CONDITION MONITORING?
Condition monitoring is a proactive maintenance strategy that involves the continous monitoring of equipment and systems to detect potential faults or deviations from normal operating conditions. It is a key component of predictive maintenance, aiming to identify issues before they lead to equipment failure and costly downtime.
By monitoring various parameters such as vibration, temperature, humidity and more, condition monitoring helps businesses optimize their maintenance efforts and maximize equipment reliability and performance.
HOW DOES CONDITION MONITORING WORK?
Condition monitoring relies on the collection and analysis of data from various sensors and monitoring devices. These devices are strategically placed on equipment to measure parameters such as vibration, temperature, pressure, electrical signals, and more. The collected data is then analyzed to identify anomalies, patterns, and trends that indicate potential faults or deviations from normal operating conditions.
The process of condition monitoring typically involves the following steps:
- Sensor Placement: Sensors are installed on the equipment in critical areas or positions where they can capture relevant data. The selection of sensor types and their optimal placement depends on the specific equipment and the parameters to be monitored.
- Data Collection: Sensors continuously gather data on the select parameters. This data can be collected in real-time or at regular intervals, depending on the monitoring system.
- Data Analysis: The collected data is analyzed using specialized software or algorithms to compare data with historical trends to help identify anomalies, patterns or indictors of potential issues.
- Alert Generation: When the analysis detects abnormal behavior or potential faults, alerts or notifications are generated to inform maintenance personnel. These alerts can be transmitted via email, SMS, or dedicated monitoring software.
- Maintenance Actions: Proactive maintenance can be implemented to prevent failures and optimize the overall maintenance strategy.
.jpg?width=750&height=146&name=Vibration%20Temp%20Pressure%20Icons%20(1).jpg)
TYPES OF CONDITION MONITORING
Condition monitoring encompasses various techniques and parameters to access the health and performance of equipment. Here are some of the most commonly used types of condition monitoring:
- Vibration Monitoring: Vibration analysis is a widely employed technique for monitoring rotating machinery. By analyzing the vibration patterns, frequencies, and amplitudes, maintenance professionals can detect imbalances, misalignments, bearing defects, and other potential issues.
- Temperature Monitoring: Temperature is a crucial parameter to monitor in any application. Abnormal temperature variations can indicate problems such as overheating, cooling system failures, or insulations issues.
- Pressure Analysis: Pressure variations can be indicative of issues in systems such as hydraulic or pneumatic equipment. Continous pressure monitoring helps identify leaks, blockages, valve malfunctions, or excessive load conditions.
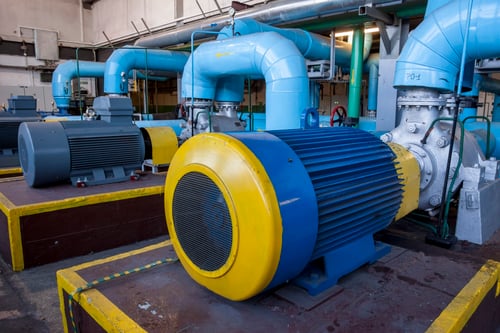
APPLICATIONS OF CONDITION MONITORING
Condition monitoring has a wide range of applications across various industries. Here are some commons applications:
- Motors: Condition monitoring plays a vital role in ensuring the reliable operation of electric motors. By monitoring parameters such as vibration, temperature, and electrical parameters, potential motor faults can be detected early, avoiding unplanned downtime and optimizing maintenance schedules.
- Pumps: Pump failure can have significant consequences in industries such as manufacturing, oil and gas, and water treatment. Condition monitoring allows for the early detection of pump issues such as bearing wear, impeller imbalances, cavitation, and seal failures.
- Fans and Blowers: Monitoring the performance and health of fans and blowers is critical for industries that rely on proper airflow, such as HVAC systems, industrial ventilation, and power generation. Condition monitoring helps identify issues such as fan blade damage, belt slippage, or motor misalignment.
- Compressors: Condition monitoring enables the detection of faults in compressors, including issues with valves, bearings, lubrication, and pressure fluctuations. Timely identifications of these problems can prevent breakdowns and improve overall system efficiency.
WIRED VS WIRELESS CONDITION MONITORING SYSTEM
Condition monitoring systems can be implemented using both wired and wireless approaches. Choosing between wired and wireless condition monitoring depends on factors such as the specific application, facility layout, and the desired level of flexibility and convenience. Below are some considerations for each:
Wireless Condition Monitoring:
- Flexibility: Wireless systems offer greater flexibility in sensor placement and system configuration, as they eliminate the need for physical wiring.
- Scalability: Wireless networks can be easily expanded and adapted to changing monitoring needs by adding or relocating sensors without the constraints of physical connections.
- Installation: Wireless systems generally have quicker and less disruptive installation processes, reducing downtime during implementation.
Wired Condition Monitoring:
- Stability: Wired systems typically provide stable and reliable data transmission since they are not susceptible to interference.
- Installation: Wired systems may require more effort and time for installation, especially in existing facilities where cable routing can be challenging.
HOW TO INTEGRATE/SETUP CONDITION MONITORING
Integrating and setting up a condition monitoring system requires careful planning and execution. Below are the key steps involved in integrating and setting up a condition monitoring system.
- Identify critical equipment and parameters based on importance, failure data and maintenance goals.
- Choose appropriate monitoring technology and sensors compatible with existing equipment.
- Place sensors strategically on equipment following guidelines and best practices.
- Implement a data collection system for regular or real-time sensor readings.
- Set baseline values and thresholds for each parameter.
- Configure the monitoring system to generate alerts or notifications for anomalies.
- Develop a maintenance plan based on insights from the monitoring system.
- Continuously review monitoring data, adjust thresholds, and optimize maintenance strategy
WHY CONDITION MONITORING?
Unplanned downtime poses a significant challenge for manufacturers, resulting in annual losses around $20 billion. Reactive maintenance practices contribute to 70% of industrial injuries. Equipment uptime directly impacts plant productivity and output, making unplanned shutdowns due to poorly maintained equipment extremely costly.
Condition monitoring is a proactive maintenance strategy that continuously monitors equipment and systems, enabling early fault detection and timely maintenance actions. By implementing condition monitoring, manufacturers can prevent unplanned downtime, maximize equipment uptime, and save substantial amounts of money. Additionally, it enhances workplace safety by reducing the likelihood of injuries associated with reactive maintenance.
FAQ
A condition monitoring sensor is a device used to measure and monitor various parameters of equipment or systems, such as vibration, temperature, pressure, or electrical signals. These sensors provide real-time data to detect abnormalities and potential faults, enabling proactive maintenance actions.
Three common types of condition monitoring techniques are vibration monitoring, temperature monitoring, and oil analysis.
-
Vibration monitoring detects irregularities in equipment by analyzing vibration patterns.
-
Temperature monitoring tracks temperature variations to identify potential issues.
-
Oil analysis assesses the quality and condition of lubricants to determine equipment health.
The five key elements of condition monitoring are data collection, data analysis, alert generation, maintenance planning, and continuous improvement. Data collection involves gathering information from sensors or monitoring devices. Data analysis analyzes the collected data for abnormal patterns. Alert generation triggers notifications when issues are detected. Maintenance planning utilizes the insights for efficient scheduling. Continuous improvement involves refining the monitoring system and maintenance strategies based on data analysis and feedback.
Examples of condition monitoring applications include monitoring the health of motors, pumps, compressors, fans, and other rotating equipment.
The five types of sensors commonly used in control systems are temperature sensors, pressure sensors, level sensors, flow sensors, and proximity sensors. These sensors provide critical input data for control systems to monitor and regulate various parameters.
Vibration monitoring is one of the most common and widely used condition monitoring techniques. It provides valuable insights into the health of rotating machinery, detecting faults such as misalignment, unbalance, bearing wear, or mechanical looseness that can lead to equipment failure.
GraceSense Predictive Maintenance System
Condition Monitoring Solution
Our suite of smart devices provide advanced analytics with deep insights about machine health to prevent unplanned downtime.
Wireless condition monitoring solution capable of providing real-time, sensor-based insights to almost any industrial application.
Advanced analytics provide asset managers with deep insights to machine health to effectively prioritize resources and maintenance spend.
Improve overall plant reliability, safety, and maintenance metrics by remotely monitoring asset health.