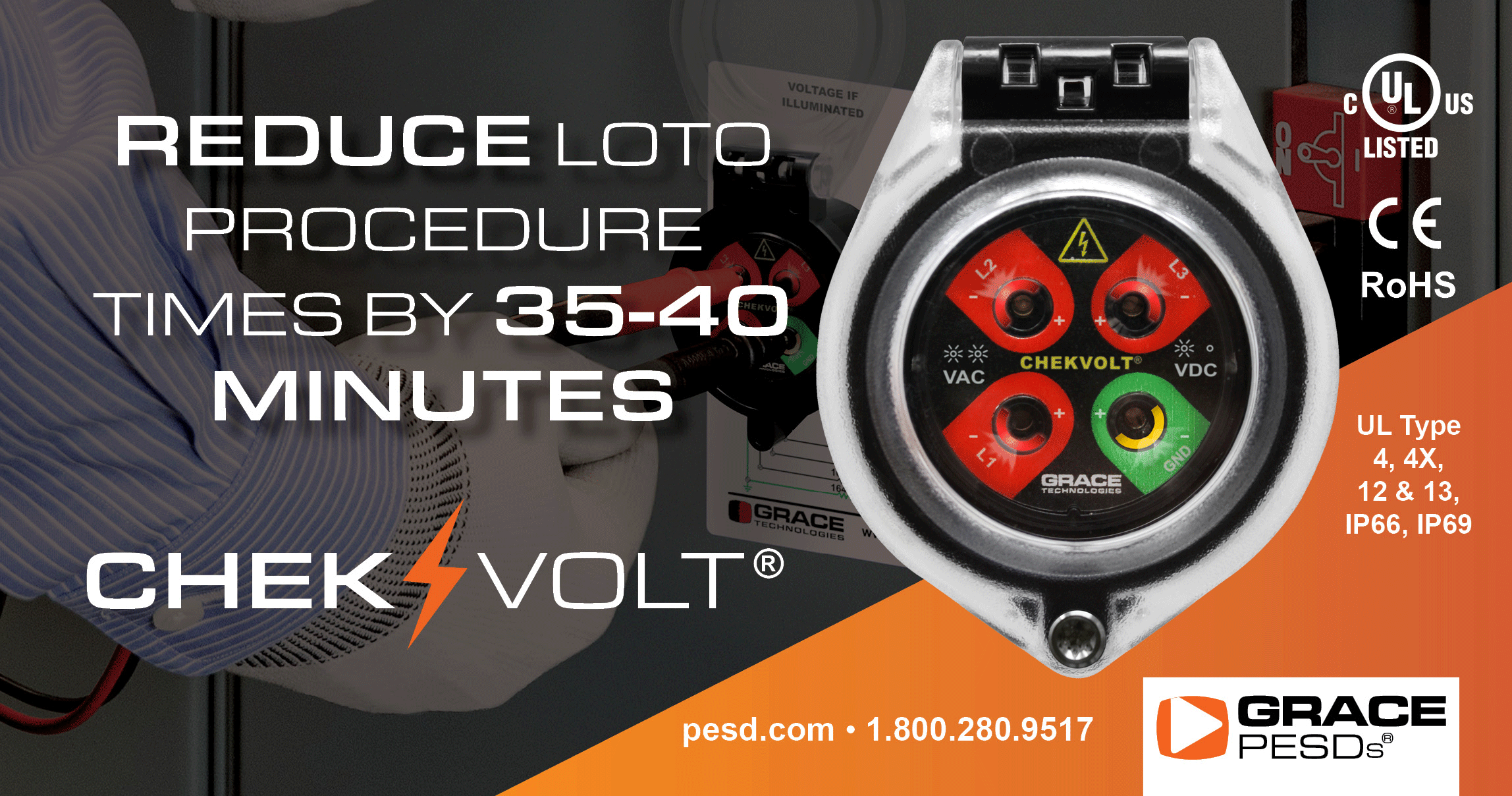
Advancing Electrical Safety: Workplace Safety, PESDs, and Predictive Maintenance
As National Electrical Safety Month draws to a close, we reflect on the importance of prioritizing electrical safety in the workplace. The risks associated with electrical hazards demand proactive measures and innovative solutions to ensure the well-being of workers and the continuity of operations. In our recent webinar on Workplace Safety, Permanent Electrical Safety Devices (PESDs), and Predictive Maintenance, we delved into key principles and technologies that can revolutionize electrical safety protocols. Join us as we recap the highlights and explore the potential of advancing electrical safety through a comprehensive approach.
Importance of Workplace Safety and Compliance
- Electrical accidents and hazards pose significant risks to workers, with severe consequences ranging from injuries to fatalities.
- Compliance with industry standards, such as NFPA 70E and OSHA regulations, is crucial to create a safe working environment.
- Proper Lockout/Tagout (LOTO) procedures, supported by comprehensive training and periodic inspections, play a vital role in mitigating electrical hazards.
- Statistics show that Control of Hazardous Energy violations continue to be a major concern, emphasizing the need for strict adherence to energy control programs and training.
Permanent Electrical Safety Devices (PESDs)
- PESDs, such as voltage LED indicators and high impedance-protected test points like ChekVolt and Safe-Test Point, enhance safety and efficiency during LOTO procedures.
- These devices provide visual confirmation of voltage presence, reducing the risk of accidental energization.
- PESDs enable qualified electricians to perform absence of voltage tests safely and efficiently from outside the enclosures, complying with NFPA 70E guidelines.
- By reducing LOTO procedure times by 35-40 minutes, PESDs improve compliance, productivity, and cost-effectiveness, making them a valuable addition to electrical safety programs.
Preventing Unplanned Downtime with Predictive Maintenance
- Unplanned downtime poses significant risks and financial losses to organizations.
- Reactive maintenance, commonly associated with unplanned downtime, is responsible for a high percentage of electrical injuries.
- Integrating predictive maintenance solutions, such as the GraceSense Predictive Maintenance System, allows proactive monitoring of critical equipment to identify potential issues before they escalate.
- Continuous monitoring of electrical assets, such as motors and connections, helps prevent failures, reduce unplanned downtime, and enhance safety by minimizing the occurrence of reactive maintenance scenarios.
As we conclude National Electrical Safety Month, we urge organizations to prioritize workplace safety and embrace advanced technologies to mitigate electrical risks. By incorporating PESDs and implementing predictive maintenance strategies, companies can enhance compliance, prevent injuries, and increase productivity. Together, let's embark on the journey of advancing electrical safety, improving workplace conditions, and unlocking the potential of IIoT predictive maintenance technologies. Stay safe, stay proactive, and secure a brighter future for your workforce.
Remember, electrical safety is an ongoing commitment. Explore our website for more resources, previous blogs, and solutions to empower your electrical safety initiatives. Ready to take the next step towards enhanced electrical safety? Request your ChekVolt PESD sample today and experience the difference firsthand. Don't compromise on safety and efficiency – fill out the form now to get started. A safer tomorrow is just a click away!